삼성전기, 차세대 반도체 패키징 공정 '승부수'
제품 두께 30~40% 얇아지고 전력·속도 개선… 디자인도 영향
내년 모바일 AP에 본격 적용… 기판 사업 '적자 늪' 탈출 노려
대만 TSMC, 팬아웃 기술로…작년 얇아진 아이폰7 두뇌 공급
전자업계 관계자는 16일 “삼성전기의 팬아웃 공정이 하반기 소형 IC칩에 적용된다”며 “모바일 애플리케이션프로세서(AP)에는 내년부터 적용 가능할 것”이라고 말했다. 지난해 7월 관련 생산라인 구축에 2632억원을 투자한 삼성전기는 1000억원 안팎의 추가 투자도 검토 중인 것으로 전해졌다.
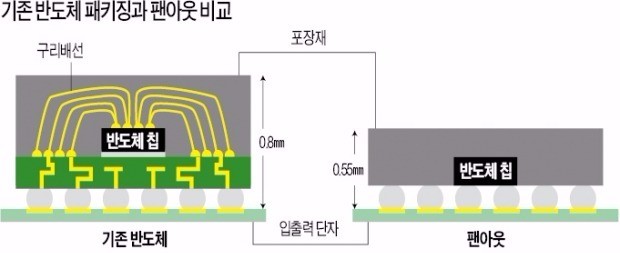
반도체 제조는 반도체 자체를 생산하는 전(前)공정과 생산된 반도체를 보호하는 물질을 씌우고 입출력 단자를 연결하는 후공정으로 나뉜다. 최근까지 반도체산업의 혁신은 전공정에서 이뤄졌다. 공정 미세화를 통해 똑같은 면적의 실리콘 웨이퍼에서 더 많은 반도체를 생산해 반도체 제조단가를 낮추고 메모리 집적도를 높이는 게 화두였다.
하지만 최근 반도체 집적도가 20나노미터(㎚, 1㎚=10억분의 1m) 아래까지 떨어지며 공정 미세화는 한계에 부딪혔다. 공정에 영향을 주는 변수가 늘면서 미세화에 들어가는 비용이 높아져서다.
이 과정에서 각광받은 것이 후공정의 팬아웃 기술이다. 기존 반도체는 인쇄회로기판(PCB) 위에 반도체를 올리고 하단의 입출력 단자를 구리선으로 연결해 완성했다. 미세화로 반도체 크기를 줄여도 입출력단자 때문에 후공정이 끝난 반도체 제품 크기에는 별반 차이가 없었다. PCB 면적 내에 입출력단자를 배치한다는 점에서 팬인(fan in)으로 불린다. 하지만 팬아웃은 PCB를 없애고 반도체와 입출력단자를 바로 구리선으로 연결해 만든다.
이렇게 하면 PCB 두께만큼 반도체 제품 두께가 30~40% 얇아진다. 입출력 단자와 반도체를 연결하는 구리선 거리도 짧아져 소모 전력과 속도도 개선된다. 반도체칩의 성능이 높아지면서 칩 하나에 들어가는 입출력 단자 수도 늘어난다. 팬아웃 기술을 이용하면 두세 배까지 연결 단자 수를 늘릴 수 있다. PCB가 후공정 재료에서 사라지면서 수율만 높아지면 원가도 떨어진다. 고정된 PCB 판 위에 반도체가 올라가는 것이 아니기 때문에 반도체를 다양한 방식으로 제품에 붙일 수 있어 전자제품의 디자인에도 영향을 미친다.
◆기판사업 반전 승부수
삼성전기는 후공정 사업을 통해 기판사업 부진을 만회한다는 전략이다. 삼성전기의 핵심 사업이던 기판은 2014년부터 손실이 불어나 지난해에 369억원의 영업손실을 입었다. 매출 규모도 계속 줄고 있다. 업계 관계자는 “기판 경쟁력의 핵심인 두께 등에서 국내 중견업체 및 중국업체들과의 기술 격차가 거의 사라진 탓”이라며 “팬아웃 후공정이 확산되며 반도체 PCB 시장마저 줄어들면 사업부의 존립 자체가 위태로울 수 있다”고 말했다.
팬아웃 후공정에서 삼성전기는 후발주자다. 세계 최대 파운드리(반도체 수탁생산 업체)인 대만의 TSMC는 이미 지난해 팬아웃 기술을 활용해 애플 아이폰7에 스마트폰 AP를 공급했다. 팬아웃으로 모바일 AP가 만들어지면서 아이폰7의 두께도 경쟁 스마트폰보다 얇아졌다는 분석이다.
삼성전기는 지난해 하반기부터 이윤태 사장 직할 조직으로 팬아웃개발팀을 신설하고 삼성전자에서 관련 연구인력도 영입했다. 올해 소형 IC를 팬아웃으로 제조하면서 처음 매출에 반영된다. 내년부터는 부가가치가 높은 스마트폰 AP까지 공정 적용이 확대돼 수익성 개선에도 도움을 줄 전망이다.
노경목 기자 autonomy@hankyung.com
-
기사 스크랩
-
공유
-
프린트