[경쟁력이 힘이다] 현대중공업, 3D 스캐너로 3㎜ 오차도 잡아낸다…기존보다 해상도 2배 높인 선박용 레이더도 개발
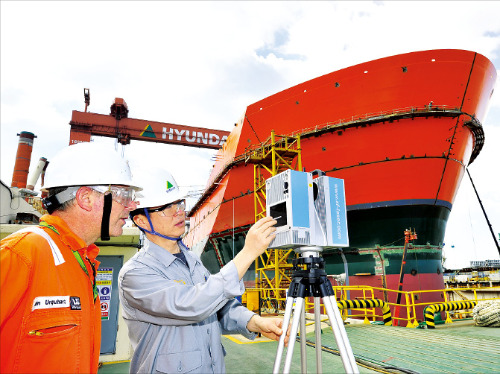
![[경쟁력이 힘이다] 현대중공업, 3D 스캐너로 3㎜ 오차도 잡아낸다…기존보다 해상도 2배 높인 선박용 레이더도 개발](https://img.hankyung.com/photo/201311/AA.8025588.1.jpg)
현대중공업은 이 제품을 현재 개발 중인 선박통합운영시스템 ‘스마트십 2.0’과 연계할 계획이다. 스마트십 2.0은 선박의 운항시스템, 환경정보 등을 종합해 기관장치에 적용하는 시스템이다. 선박이 경제적이고 안전한 운항을 할 수 있게 도와준다.
현대중공업은 선박 건조과정에도 최신 정보기술(IT)을 도입했다. 최대 수백미터 크기의 초대형 선박과 해양구조물을 건조할 땐 설계와 실제 제품간의 오차를 측정하는 게 무엇보다 중요하다. 초대형 선박과 극한의 기후에서 운용되는 해양구조물에서는 단 몇 ㎜의 오차가 큰 사고로 이어질 수 있다.
현대중공업은 최근 3D 스캔 기술을 활용, 부유식 원유생산·저장·하역설비(FPSO)의 오차 측정을 마쳤다. 3D스캐닝 기술이란 3㎜ 간격의 레이저를 선박에 쏴 얻은 디지털 정보로 입체영상을 만드는 것으로 문화재를 측정할 때 많이 사용하는 방식이다. 이 기술을 사용하면 자동으로 해양 구조물의 입체영상을 만들 수 있고 설계 도면과 비교해 오차도 분석할 수 있다. 회사 관계자는 “새로운 기술을 도입하면서 해양구조물 1개당 오차 측정시간을 10시간에서 2시간으로 줄였다”고 설명했다. 두개의 블록을 미리 영상으로 합쳐볼 수도 있어 조립 과정에서 벌어질 문제점을 미리 알 수 있는 장점이 있다.
현대중공업이 지난달 10일 수주한 모스형 액화천연가스(LNG) 운반선에도 신기술이 들어가 있다. 모스형 LNG선이란 동그란 반구 형태의 탱크가 탑재된 LNG선을 말한다. 네모난 형태의 멤브레인형 LNG선에 비해 가격은 비싸지만 안전성이 뛰어나다는 장점이 있다. 현대중공업은 12년 만에 이 배를 수주했다. LNG선은 15만㎥ 이상의 LNG를 한번에 실을 수 있고 척당 2억달러가 넘는 고부가가치 선이다.
이 배를 발주한 말레이시아 국영 에너지기업 페트로나스는 선박의 안전성을 최우선으로 여겨 최근의 ‘대세’인 멤브레인형보다 모스형을 선호한 것으로 알려졌다. 현대중공업이 가진 풍부한 건조 경험과 설계 능력 등이 높은 평가를 받았다는 후문이다.
김대훈 기자 daepun@hankyung.com
-
기사 스크랩
-
공유
-
프린트