"산·학·연에 스마트 팩토리 기술 공유"…포항제철소, 스마트공장 확산 앞장
스마트공장 구축·역량강화 지원
UNIST, 딥러닝 알고리즘 활용
고로 조업 예측 모델 개발 기여
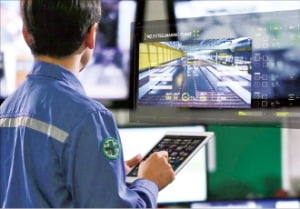
포항제철소는 2015년부터 포항 2열연공장을 시작으로 스마트 팩토리 구축 사업에 나서 제철소 각 공장에서 생성되는 조업 데이터 등을 실시간 수집해 모든 공정으로 스마트 팩토리를 확대할 수 있는 인프라 기반을 마련했다. 지난해까지 140여 건의 스마트 팩토리 과제를 공정별로 추진해 현장에 적용했다.
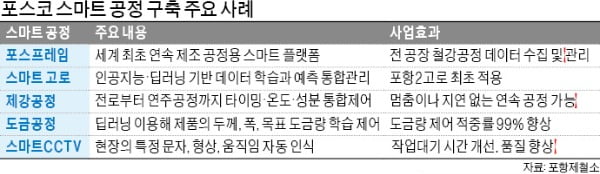
포항 2, 4연주공장은 표면 결함 예측이 가능한 인공지능 모델을 구축해 연간 6억원 이상의 원가를 절감하고 있다. 딥러닝 기술을 이용해 도금 정확도를 89%에서 99%까지 높인 초정밀 도금 제어 기술도 있다.
포항제철소는 2023년까지 200억원을 들여 중소기업 1000여 개를 대상으로 상생형 스마트 팩토리 지원사업에 나서기로 했다. 이 사업은 ‘상생형 스마트공장 구축지원 사업’과 ‘스마트화 역량강화 컨설팅’으로 구성된다. 포스코는 스마트공장 구축과 혁신컨설팅을 패키지로 제공함으로써 중소기업이 체계적으로 스마트공장을 구축하고 운영할 수 있도록 돕는다.
상생형 스마트공장은 스마트 팩토리를 도입한 25개사를 대상으로 조사한 결과 스마트 사업이 적용된 설비 및 공정에서 생산성과 품질은 각각 43%와 52% 증가하고, 비용과 납기는 27%가량 줄어든 효과를 거둔 것으로 분석됐다.
자동차 부품업체인 동국산업(대표 안상철)은 포스코와 인공지능 기반 산화물 제어 프로그램을 구축해 열연코일을 소재로 자동차부품용 고합금강을 생산하는 과정에서 산화물의 빠른 제거로 생산성을 60% 높이는 효과로 이어졌다. 부산의 선박엔진부품 수리업체 종합폴스타(대표 김철규)는 포스코의 스마트공장 지원사업으로 수작업하던 모든 제품의 공정 관리를 QR코드 시스템으로 바꿨다.
중소기업과 대학 등 산·학·연에 전수한 스마트 팩토리 기술은 포항제철의 경쟁력을 높이는 결과를 낳고 있다. 최재식 UNIST 전기전자컴퓨터공학부 교수는 실시간 데이터 기반으로 딥러닝 알고리즘을 활용해 고로 조업을 예측하는 모델을 개발한 것을 기반으로 대형 고로 확대 적용에도 참여, 딥러닝 모델의 정합성을 높이는 데 기여하고 있다.
포항=하인식 기자 hais@hankyung.com
-
기사 스크랩
-
공유
-
프린트