전자부품연구원, 2년간 1만개 시험품 평가…국산화·수출 전방위 지원
(5) 전자부품연구원
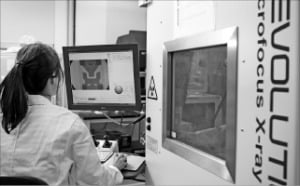
전자부품연구원은 국내 기업이 개발한 소재·부품의 신뢰성을 평가하고 인증해 국산화는 물론 해외 판로 개척을 지원하고 있다.
엠케이전자의 은합금본딩와이어가 대표적 사례다. 본딩와이어는 반도체와 발광다이오드(LED) 생산에 없어선 안 되는 핵심 소재다. 전기적 신호를 전달하는 미세선으로, 굵기가 머리카락 5분의 1 정도인데도 고열에서 오래 견딜 수 있어야 해 높은 기술력이 요구된다. 본딩와이어는 통상 열전도가 잘 되고 강도가 높은 금을 사용해 원가가 높다. 그래서 최근에는 구리나 은합금을 재료로 하는 본딩와이어의 수요가 커지고 있다.
엠케이전자는 2014년 은합금본딩와이어 생산에 성공했다. 당시엔 세계 점유율 1위인 일본 다나카전자공업이 은합금본딩와이어 생산을 독점하다시피 하고 있었다. 엠케이전자 관계자는 “현재 은합금본딩와이어 분야에서 엠케이전자의 국내 점유율은 80%가량으로 거의 국산화됐다”며 “해외 시장 점유율에서도 다나카전자공업과 어깨를 나란히 하고 있다”고 말했다.
이 같은 성과의 배경에는 전자부품연구원의 신뢰성 평가가 있었다. 2년간 1만 개 넘는 시험품을 제작해 신뢰성 시험, 재료 분석 등을 지원했다. 수요기업인 씨티엘(현 씨티젠)과 컨소시엄을 구성했기에 가능한 일이었다. 마병진 수석연구원은 “반도체와 LED 공정은 워낙 미세하고 복잡해 부품 및 소재를 개발해도 신뢰성이 확보되지 않으면 실제 공정에 투입되기 힘들다”며 “처음부터 양산을 염두에 두고 수요기업과 함께 신뢰성평가를 한 게 좋은 결과를 낳았다”고 설명했다.
버스 택시 지하철 등 교통시스템 단말기 생산기업인 에이텍티엔은 전자부품연구원의 신뢰성 평가와 솔루션을 바탕으로 해외시장을 뚫었다. 수출 대상국 환경에 맞춰 내구성을 높일 수 있도록 종합 컨설팅을 지원한 것이다. 이후 에이텍티엔은 몽골, 말레이시아, 코트디부아르 등과 고속버스 단말기 수출계약을 맺었다.
구은서 기자 koo@hankyung.com
-
기사 스크랩
-
공유
-
프린트