지멘스, 빅데이터 활용해 공장 자동화…불량률 0.001%
문제 생기면 컴퓨터가 즉시 알려
직원이 원격제어로 1분 내 해결
자동화율 75%…생산성 8배↑
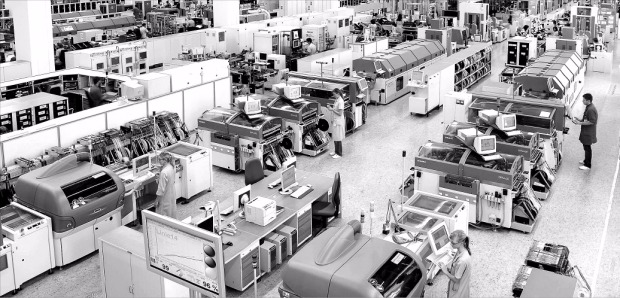
○디지털화로 빅데이터 자동 분석
암베르크 공장에서 생성되는 데이터는 매일 5000만건에 달한다. 개별 바코드로 분류된 부품과 설비들이 기계 이상과 불량품 등을 감지하는 1000여개의 센서와 스캐너를 통해 막대한 양의 데이터를 쏟아낸다.
디지털화된 시스템은 이 데이터를 생산공정 개선과 공장 자동화를 위한 정보로 재가공해 알려준다. 어떤 공정에서 문제가 발생하면 컴퓨터는 담당자에게 바로 이메일을 보낸다. 담당자는 원격제어를 통해 문제를 해결한다. 멈춰선 라인을 재가동하는 데는 채 1분이 걸리지 않는다.
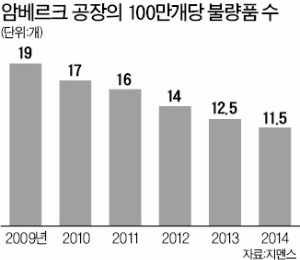
슈테판 리첼 암베르크 공장 생산엔지니어링부장은 “빅데이터를 활용한 공장 자동화 시스템을 구축하기 위해 2억유로(약 2331억원)를 투자했다”며 “생산공정 개선으로 불량률은 제품 100만개 가운데 11.5개 수준으로 줄었고 생산성은 8배 증가했다”고 강조했다. 불량률은 25년 전의 40분의 1 수준이다.
○사람에 기반한 자동화
이 공장의 자동화율은 75%를 넘는다. 현장 직원들은 불량으로 판명된 제품을 테스트하거나 중요한 의사결정을 내리는 등 생산 전략을 수립하는 업무만 담당한다.
랄프 프랑케 지멘스 공장자동화사업부 사장은 “지멘스의 목표는 자동화가 아니라 비용과 품질을 고려한 최적화”라며 “100%의 자동화가 아니라 사람이 할 때 효율적인 업무와 기계가 할 때 효율적인 업무를 구분해야 한다”고 말했다.
그는 “기계와 인간을 이어주는 자동화를 구현하고 실수를 개선하기 위해서는 현장의 목소리에 귀를 기울여야 한다”며 “지난해 현장에서 제안한 아이디어가 1만건에 달했다”고 했다. 지멘스는 직원들의 공장 자동화 관련 아이디어를 수시로 접수해 채택될 경우 건당 3600유로(약 480만원)를 지급하고 있다.
소프트웨어에 대한 강조도 이어졌다. 시몬 빌란트 암베르크 공장 매니저는 “앞으로 다가올 제조업 혁신의 핵심은 상품 설계를 위한 아이디어 단계부터 생산까지의 모든 정보를 효율적으로 관리하는 제품수명주기관리(PLM) 시스템 등의 소프트웨어(SW) 기술”이라며 “지멘스는 매년 이익의 20%를 SW 부문에 투자하고 있다”고 강조했다.
암베르크=김순신 기자 soonsin2@hankyung.com
-
기사 스크랩
-
공유
-
프린트