신기술 개발 '유레카'의 순간마다 통념을 깨는 '발칙한' 상상이 있었다
삼성전자 3D낸드플래시
초고층 건설 기술 활용, 셀 수직으로 쌓는데 성공
SK케미칼 PPS
설탕없이 단맛 가능하듯 염소 빼고 플라스틱 만들어
효성 폴리케톤
모두 반대하던 금속염 첨가, 신참 연구원 고집으로 성사
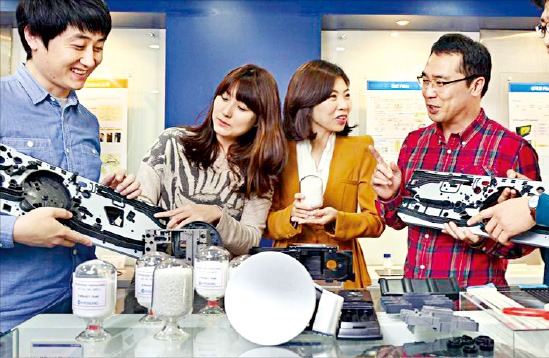
“몇 년 동안 끙끙대던 문제를 한순간에 번뜩이는 아이디어로 해결하는 경우가 있습니다. 이렇게 ‘유레카(알아냈어)’를 외치는 순간들을 여러 차례 거치면서 신기술 개발이 결실을 맺지요.”
최근 나일론에 버금가는 신소재로 평가받는 폴리케톤을 10년 만에 상용화한 효성의 이원 전무가 들려준 말이다. 엔지니어들이 새로운 공법이나 물질을 내놓는 과정을 살펴보면 의외의 곳에서 돌파구를 찾는 드라마틱한 경우가 종종 있다.
○건축 기술이 반도체 기술로
‘삼성전자가 삼성물산에서 반도체 기술을 배웠다?’
삼성전자가 최근 세계 최초로 양산을 시작한 3차원(3D) 낸드플래시 반도체의 숨은 공신은 뜻밖에도 삼성물산 건설부문이다. 셀을 24층으로 쌓아 3D 낸드를 만드는 과정에서 세계 최고 높이(828m)의 ‘부르즈 칼리파’를 세운 삼성물산의 노하우를 전수받은 것이다.
3D 낸드는 기존 미세공정으로 셀 간격을 좁힌 게 아니라 셀을 위로 쌓아 집적도를 높인 제품이다. 삼성전자는 1990년대부터 미세공정 기술과 함께 셀을 위로 쌓는 기술도 연구해왔다. 그러나 20나노대까지는 셀 간격을 줄이는 게 더 효율적이고 기술 개발도 빨랐다.
작년부터 미세공정이 10나노대에 들어서자 문제가 생겼다. 셀 간격이 너무 좁아지자 전자 간섭이 발생하며 성능이 떨어지는 현상이 빚어졌다. 미세공정이 물리적 한계에 부딪히자 삼성전자는 3D 낸드 개발에 본격적으로 착수했다. 3D 낸드를 만들려면 셀을 쌓기 쉽게 기존의 직각 형태가 아닌 원통형으로 만들어야 했다. 또 이를 위로 쌓는 3차원 수직적층 기술도 필요했다. 하지만 아주 작은 셀을 위로 쌓다 보니 쉽게 넘어지는 문제가 생겼다. 또 ‘플로어’라고 부르는 토대에 24층 수직으로 쌓은 셀을 꽂기 위해 25억개의 정밀한 구멍을 뚫어야 했다.
삼성전자가 컨설팅받은 게 바로 이 부분이다. 삼성물산은 부르즈 칼리파와 타이베이101, 페트로나스타워까지 세계 3대 초고층 빌딩을 건설하며 위로 쌓는 기술은 세계 최고 수준이다. 부르즈 칼리파를 지을 때는 사흘에 한 층씩 올리며, 배관으로 콘크리트를 601m나 단숨에 올려보내는 초고층 펌핑 기술을 개발하기도 했다. 삼성전자 관계자는 “삼성물산에서 빌딩을 쌓을 때 흔들리는 정도, 오차 범위 등을 계산하고 감안해 층을 올리는 법 등을 배웠다”며 “쌓인 셀을 플로어에 넣기 위해 구멍을 내는 데도 도움을 받았다”고 말했다.
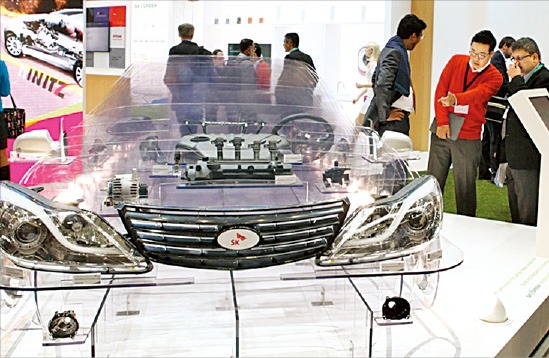
○상식을 깨는 아이디어가 돌파구
수많은 재료를 혼합하는 과정을 거쳐 탄생하는 화학 물질은 실험 과정에서 의외의 결과물로 얻는 경우가 많다. SK케미칼이 개발한 공업용 플라스틱 소재인 PPS(폴리페닐렌 설파이드)가 대표적이다. 섭씨 250도의 고온에도 견디는 PPS는 자동차와 전자제품 등에서 금속을 대체할 소재로 각광받고 있다. 미국과 일본 기업들이 독식하고 있는 PPS 시장에 SK케미칼은 유해한 염소를 사용하지 않은 친환경 제품으로 주목받고 있다.
경쟁사들은 벤젠에 염소를 합성한 ‘P-디클로로벤젠’이라는 물질을 사용해 PPS를 만든다. 이 물질을 첨가해 ‘벤젠→클로로벤젠→디클로로벤젠→PPS’로 제품이 나오는 구조다. SK케미칼 관계자는 “제조 과정에서 염소를 넣었다가 제거하는 과정을 반복하게 되는데, 아예 처음부터 염소없이 만들 수도 있지 않을까라는 아이디어가 나왔다”며 “1년 동안 연구한 끝에 벤젠에 특정 물질을 결합해 염소처리 과정을 생략하고 PPS를 만드는 공정을 개발했다”고 소개했다. SK 측은 “단맛을 내려면 당연히 설탕을 넣어야 한다고 생각하던 것을 뒤엎은 것과 비슷하다”고 설명했다.
효성이 지난 4일 선보인 공업용 플라스틱 소재인 폴리케톤은 신참 연구원의 아이디어가 결정적인 기여를 했다. 1980년대부터 미국 독일 등 기업들이 상용화에 도전했던 폴리케톤은 가공 과정의 안정성이 문제가 돼 제품으로 연결되지 못하던 소재였다. 2004년 개발에 착수한 효성 연구진은 수천가지 안정제를 대상으로 실험을 시작했다. 식품첨가제로 범위를 확대한 연구진은 금속염이 포함된 물질은 폴리케톤 공정에 방해가 된다는 연구결과를 믿고 금속염 관련 물질은 모두 배제했다.
효성 관계자는 “어느날 한 연구원이 금속염 성분이 있는 첨가제도 적용해보자는 의견을 냈지만 받아들여지지 않았다”며 “그 연구원은 혼자 며칠을 씨름한 끝에 안정성을 획기적으로 높이는 결과를 얻어냈고 수차례 추가 실험을 통해 신뢰성이 입증됐다”고 설명했다.
박해영/김현석 기자 bono@hankyung.com
-
기사 스크랩
-
공유
-
프린트