'재활용 시멘트' 탄소 20% 줄였다
-
기사 스크랩
-
공유
-
댓글
-
클린뷰
-
프린트
현장 르포
오스트리아 홀심 시멘트 공장
유럽선 폐건자재 시멘트 원료로
1t생산에 車 탄소 10만대분 감축
국내 기업은 '혼합재 규제' 묶여
오스트리아 홀심 시멘트 공장
유럽선 폐건자재 시멘트 원료로
1t생산에 車 탄소 10만대분 감축
국내 기업은 '혼합재 규제' 묶여
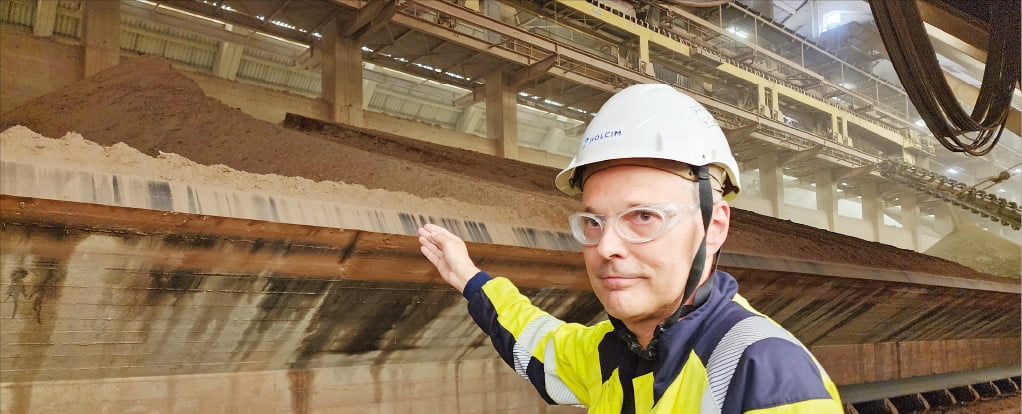
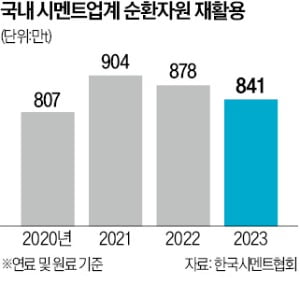
홀심시멘트가 온실가스 배출을 줄일 수 있었던 비결 중 하나는 클링커 제조 시 부원료로 폐건자재를 사용한 것이다. 베르톨트 크렌 홀심시멘트 대표는 “연구개발(R&D)을 지속해 성능은 유지하면서 이산화탄소 배출량을 줄일 수 있는 방법을 찾고 있다”며 “그 결과 클링커 제조 공정에서부터 폐건자재 사용 비율을 16%까지 올렸다”고 설명했다. 홀심시멘트는 여기에 더해 최종 제품인 시멘트를 생산할 때도 대체원료 비중을 25%까지 늘렸다. 시멘트를 석회석으로만 만든다는 고정 관념을 깨고, 고로슬래그(제철소 고로에서 나온 부산물) 등 혼합재 사용 비중을 늘리면서 탄소 배출을 줄이고 있다.
폐건자재를 시멘트 원료로 쓰는 건 오스트리아만의 특수 사례가 아니다. 지난 20일 찾은 그리스 테살로니키 타이탄시멘트 공장도 2017년부터 폐콘크리트 등 다양한 혼합재를 시멘트 원료로 쓰고 있었다.
이처럼 유럽 시멘트 생산 현장에선 친환경 기술 접목이 확산되는 추세다. 시멘트 생산 시 초고온 가열 과정이 필요한데 이때 연료로 유연탄 대신 폐플라스틱, 폐타이어 등의 비중을 높여 화석연료를 태울 때 발생하는 온실가스를 줄인다. 국내 시멘트산업에서 순환자원 재활용률이 35% 수준에 머물 때 홀심시멘트는 90%까지 늘렸다.
유럽에서는 시멘트에 사용할 수 있는 혼합재 종류(10종)가 다양하고, 비중도 36%에 달한다. 반면 국내에선 고로슬래그, 플라이애시, 포졸란, 석회석 미분말 중에서 두 종류만 제한적으로 넣을 수 있고 비중도 10%에 묶여 있다. 김진만 공주대 건축공학과 교수는 “성능이 비슷하다면 국내 시멘트업계의 탄소중립 실현을 위해 적극적인 KS 기준 완화를 검토해야 한다”고 강조했다.
매너스도르프·테살로니키=최형창 기자 calling@hankyung.com