[경북형 4차 산업혁명 현장] 위기의 한국 제조업 돌파구는 스마트팩토리
모든 공정에 디스플레이 장착
공정·가동률 등 실시간 파악
스마트팩토리 도입 후 매출 늘어
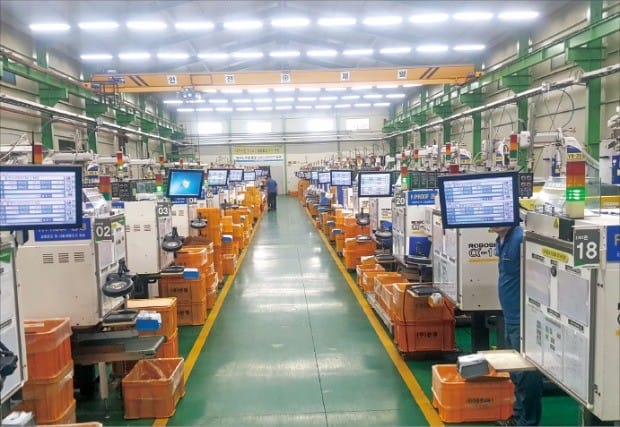
이 회사 김모 사장은 “보통 사출기 한 대에 한 명이 사람이 붙는데 38대의 장비가 있는 사출 라인에는 세 명만이 일한다”고 말했다.
6만㎡의 공장에 있는 수백 개의 라인에 로봇과 사람이 협력해 일을 하고 있지만 이 공장에는 아주 특이한 풍경이 있다. 모든 공정에 센서와 스캐너 디스플레이가 장착돼 공정마다 생산성과 작업량을 자동적으로 체크해준다. 회사 중간 천장 부근에는 대형 디스플레이 3대가 공장 전체 상황을 일일이 체크해 알려준다. 이 데이터는 현장뿐만 아니라 사무실 관리직원들에게도 실시간 중계된다. 생산목표와 시작 시간, 작업 완료예상 시간, 생산실적과 달성률, 생산성, 불량률이 자동으로 기록돼 작업자에게 보여진다. 중간중간 설치된 검사장비는 센서와 스캐너가 부착돼 불량 발생을 즉각적으로 알아내고 따로 분류한다. 어떤 부분에서 불량이 많이 생기고, 왜 생겼는지까지 정밀하게 추적할 수 있다.
공장 내 모든 기계가 통합운영 소프트웨어와 연결돼있고 모든 제품에는 바코드가 붙어있어 언제, 누가, 어느 라인에서 생산됐는지, 몇 개가 생산됐는지가 모두 자동으로 기록돼 통합운영소프트웨어에서 실시간으로 보여진다. 공장을 나오니 현황판에 공장가동률 96.8% 사출 100%, 프레스 91%, 용접 96%, 조립 100%라는 실적과 오늘 일어난 생산, 구매, 품질 등 분야별 문제내용과 조치사항이 적혀있다. 볼트하나 너트하나까지 모두 관리될 정도로 이 공장에서는 빈틈이 보이지 않았다.
김 사장은 이런 스마트팩토리화를 진행하는 데 2011년부터 50억원 이상을 투자했다. 하지만 전혀 아깝지가 않았다. 생산능률이 향상됐을 뿐 아니라 글로벌 거래처를 확보할 수 있었기 때문이다. 자동차업계가 수주물량 감소로 최악의 경기를 맞고 있지만 이 회사 매출은 3년 연속 상승세다.
김 사장이 2011년 스마트팩토리화의 시초가 된 MRP(자재구매관리 전산시스템)에 투자하려하자 주위에서는 “쥐꼬리만 한 회사가 별짓을 다한다”며 비아냥거렸다. 하지만 김 사장의 혜안과 투자 덕분에 이 회사에서 일하는 300여 명의 직원은 최악의 불경기에도 걱정없이 행복하게 일하고 있다.
김 사장은 스마트팩토리화를 추진한 이유에 대해 “기존 전사적자원관리(ERP)로는 증가하는 회사 아이템 관리를 효율적으로 할 수 없었다”며 “보다 체계적인 관리가 필요했다”고 말했다. 김 사장의 결정으로 이 회사는 5년간 현장의 POP시스템부터 MES(공정관리시스템), QMS, PMS, SAP 등을 차례로 도입하고 현재는 스마트팩토리의 고도화를 진행 중이다.
김 사장은 “사람 손이 가면 데이터 오류가 따라다녔다”며 “살아있는 데이터를 관리자들이 실시간 공유하는 환경을 만든다면 현장의 생산자들과 똑같은 데이터를 보면서 소통하고 그 과정에서 부서 간 정보의 전달 오류, 눈에 안보이는 업무의 벽에 가린 낭비요인을 찾아 숨은 부가가치를 높일 수 있겠다고 생각해 한 투자였다”고 말했다.
이 회사는 스마트팩토리화로 로봇 도입이 크게 늘었지만 2012년 이후 매년 5% 이상의 인력을 새로 뽑고 있다. 공정 자체 인력은 줄었지만 국내외 거래처가 늘어나면서 라인이 계속 늘어났기 때문이다. 이 덕택에 2016년 경상북도로부터 고용우수기업으로 선정됐다.
김 사장은 “스마트팩토리의 또 다른 효과는 지방기업의 현장직을 기피하던 현상이 사라져가고 있다는 점”이라고 말했다. 그는 “글로벌 기업의 공급체인 속으로 들어가려면 글로벌 기업의 스마트팩토리화와 수준을 같이하지 않으면 안된다”며 “앞으로 글로벌 공급체인이 많이 형성될수록 회사의 모든 생산과정 데이터를 신뢰할 수준으로 확보해야 한다”고 강조했다.
이 회사 이모 차장은 “글로벌 기업은 이제 복잡한 설명을 들으려 하지 않는다. 공정이 얼마나 표준화됐는지, 신뢰할 만한 어떤 데이터를 제시하는지 프로세스로 납품업체가 결정된다”며 “몇 년 전에는 사장님의 경영방침이 잘 이해가 되지 않았지만 이제는 스마트팩토리가 제조의 미래라는 사실을 절감한다”고 말했다.
영천=오경묵 기자 okmook@hankyung.com
-
기사 스크랩
-
공유
-
프린트