무인차가 생산제품 옮기고 전력도 자체 조달
스마트기술로 생산량 3배
불량률은 98% 감소
ESS로 전력 저장해 사용
외부 전력 없이도 공장 돌려
"중소기업의 무인공장화 적극 돕겠다"
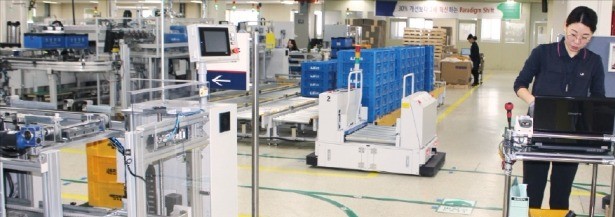
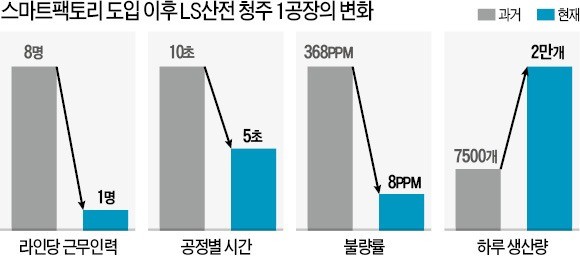
진성옥 LS산전 청주1공장 생산기술팀장은 “오는 9월부터는 완제품 검사에 한 명씩 배치돼 있는 인력도 철수해 100% 무인화가 완료될 것”이라고 설명했다. 2000년대 초반만 해도 여덟 명이 일하던 생산라인에서 생산직 근로자가 사라지는 것이다. LS산전은 이들을 신규 라인에 배치하거나 라인 관리직으로 전환해 고용을 유지할 계획이다.
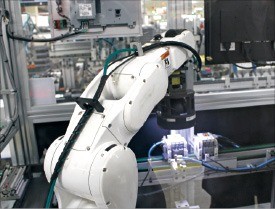
스마트팩토리는 특히 한 라인에서 여러 모델을 제조하는 혼류생산에서 강점을 보였다. 특정 모델을 생산하다 다른 모델로 생산 방식을 전환하는 데 사람은 1분 안팎이 걸리는데 스마트팩토리 설비는 제품을 인식하고 3.8초 만에 알맞은 부품을 찾아 부착한다.
1공장에서 자동차로 5분 정도 떨어진 2공장에서는 또 다른 실험을 하고 있다. 대형 변압기 등을 제조하면서 공장에서 필요한 전력의 절반을 자체 조달하는 설비를 갖췄다. 공장 지붕에서 태양광 패널을 통해 생산된 전력을 에너지저장장치(ESS)에 담았다가 사용한다. 전력 사용량이 많은 제철소 등에서 이 설비를 활용하면 외부 전력을 전혀 사용하지 않고도 공장을 돌릴 수 있다. 스마트 기술을 이용해 생산량이 늘더라도 한계비용은 0에 수렴하는 공장이 현실화되고 있다.
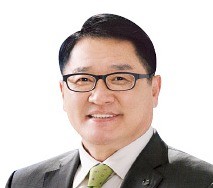
구자균 LS산전 회장(사진)은 이 같은 경험을 발판으로 스마트공장 자체를 외부에 판매하는 전략을 본격화하고 있다. 이 회사의 주력이 변압기와 전력 스위치 등 전력 인프라 관련 설비인 만큼 본업과 거리가 먼 것도 아니다. 구 회장은 “기존 사업만으로는 미래 생존을 보장받을 수 없는 만큼 스마트플랫폼을 제공하는 새로운 도전에 나서야 한다”며 “특히 정보통신 융·복합이 이뤄지고 있는 지금이 절호의 기회”라고 강조하고 있다.
LS산전은 다른 기업들이 노출을 꺼리는 생산설비를 오히려 적극적으로 개방하고 있다. 그러면서 무인설비 구축 시 비용 절감과 생산성 향상이 어떻게 일어나는지를 업종과 기업 규모에 따라 다양하게 제시하고 있다. 진 팀장은 “생산라인이 휘는 구간에서 제품 위치를 자동으로 잡아주려면 원래 수백만원짜리 일본제 설비가 필요했다”며 “우리는 휘는 각도에 맞춰 디자인된 플라스틱판을 설치해 1만분의 1 가격으로 해결했다”고 말했다. 적게는 천만원에서 수억원만 들여도 공정 효율이 향상되는 효과를 볼 수 있다는 설명이다.
중소기업 최고경영자는 물론 다른 기업 노동조합 간부들까지 와서 청주 1공장을 돌아보는 이유다. 지난해에는 중동의 한 기업이 LS산전 설비를 그대로 깔아달라고 요청하기도 했다. 초기만 해도 실현 가능성이 낮아보이던 구 회장의 스마트공장 플랫폼 구상이 현실화되고 있는 것이다.
청주=노경목 기자 autonomy@hankyung.com